WHAT YOU CAN’T SEE CAN HURT YOU
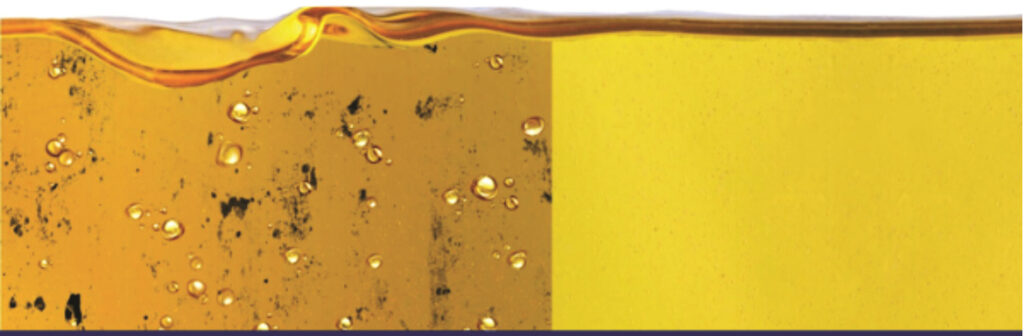
When a representative sample of lubrication oil from a lubricated piece of machinery or mechanical system is subject to rigorous oil analysis, a battery of chemical and physical tests are applied to the oil in the laboratory with some interesting (but not surprising) results.
The “spectrometric” analysis is by far the most popular form of oil analysis and is often referred to in the industry by the acronym, SOAP, which stands for Spectrometric Oil Analysis Programme and the most common instrumentation used by large laboratories is called an Inductively Coupled Plasma or ICP.
Three fundamental areas of interest engineers look for in the results of oil analysis are the:
- The health of the machine,
- The health of the oil lubricating that machine and,
- Levels of contamination found (if any).
The first two factors involving the health of the machine and the health of the lubricating oil are inextricably tied to the levels of contamination found. This is akin to the condition of a household chimney and how it can potentially impact the level of hygiene and quality of air inside that household. However, in extreme pressure and temperature conditions, like the internal combustion engine, the situation then becomes very different indeed.
The presence of these contaminants is a measure of the concentration of wear metals (machine health) and also oil additives (oil health) in the lubricating oil. This means the level of wear and tear of your engine, machine or equipment is evidenced by the amount of such (metal) contaminants found as a result of the oil analysis conducted. Further, these contaminants will alter the original specifications and properties of the lubricating oil including degradation of the host oil’s viscosity.
Leading laboratories such as WearCheck Africa measures 29 of these elements and they fall into the various categories such as copper which is a “wear” metal, calcium which forms part of an oil additive or silicon which is a constituent of dirt (contaminant) and quite a few of these elements (contaminants) can belong to more than one category.
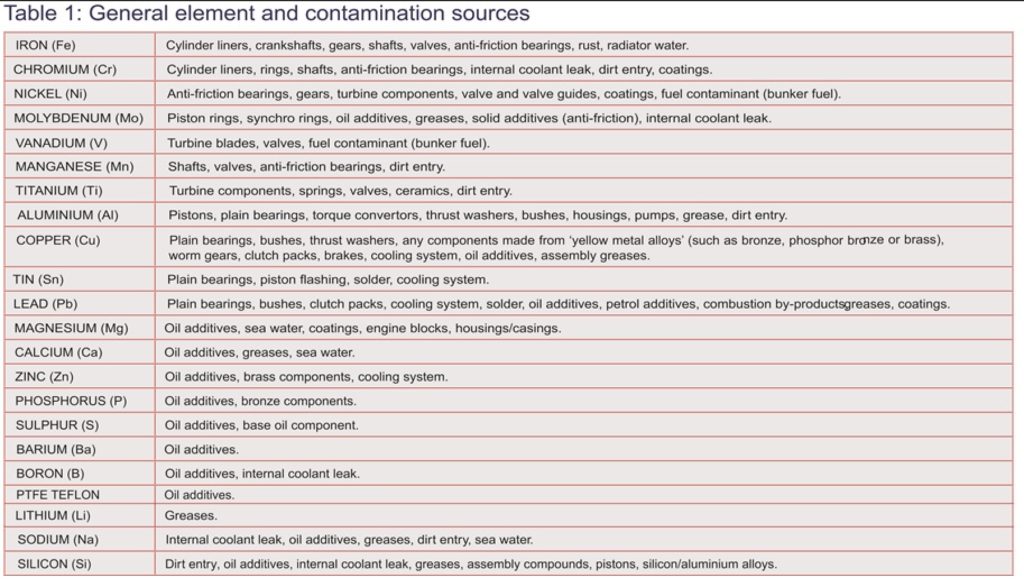
The Identification of these elements (or the contaminants) alone is not enough. In order to interpret an oil analysis report accurately, it is vitally important to know where the various elements come from and which of the three categories they can belong to. Understanding this will enable engineers to determine the wear characteristics of the machinery, identify structural weaknesses of metals and research into solutions to reduce wear, either by inventing new, more durable metals or improving the lubrication technology to reduce the coefficient of friction between interfaces in relative motion.
Fortunately, for us, WearCheck Africa has identified and categorised these elements as listed in Table 1 above. Based on the list of elements in Table 1, the contaminants typically present in lubricating oils come from the metal components of the machine itself. Parts such as cylinder liners, bearing, gears, valves, springs etc. are some of the contributors to these contaminants.
Due to the intense friction forces caused by the repetitive sliding and rolling movement of friction partners, pieces of these metal particles are shaven off, dislodged and dispersed into the lubrication oil. The continued repetition of this process eventually results in high levels of metal contaminants sediment in the lubrication oil, significantly diminishing its lubrication capabilities if not rendering it ineffective altogether as a lubricant. At this point of the lubricant oil’s lifecycle, an oil change would be the best next course of action.
Further review of Table 1 also reveals certain metal elements that also make up the main ingredient of various popular “oil additives” brands, elements such as Molybdenum, PTFE Teflon, Calcium, Silicon, etc. These elements are some of the most slippery substances known and because of this unique property, engineers have developed the technology to break down these elements into minute particles and then dispersing them into a base oil to function as lubricant enhancers.
While the idea of harnessing the lubricity of these elements seems compelling in the form of “oil additives”, these elements over time sediment in the base lubrication oil as contaminants resulting in the degradation of the base oil. Further, there have been reports that these “oil additives” being particulate, i.e. having solids dispersed in the base oil gradually agglomerate as a result of intense pressure and temperature conditions and eventually end up in the oil and fuel filters, causing clogging, compounding further the problems, resulting in unwanted additional visits to the workshop.
Of the various attempts that have been made to research into this problem of contaminants and its degrading effects on lubricating oils, Uniglide’s Friction Reducing Concentrate, a non-particulate metal treatment oil concentrate, developed from superior technology addresses this problem with a solution that not only reduces the prime cause of contaminants, i.e. friction, but also offers a solution to flush out these dispersed contaminants from the lubrication system of the machine from the very first Uniglide FRC application administered.
Visit www.uniglidemalaysia.com for more information on Uniglide FRC, the suite of products and how to apply Uniglide in engines, machines and equipment across various industries.
Acknowledgments: John Evans, WearCheck Africa, member of the Set Point Group.
© Performance Power Lubricants Malaysia Sdn Bhd is the official Distributor and Bottler of Uniglide in Malaysia
Suite 8, Lot UC -3A, Level UC, Avenue K Shopping Mall,
156 Jalan Ampang, 50450 Kuala Lumpur, Malaysia
www.uniglidemalaysia.com
WhatsApp: +6011 2771 1882